The manufacture of industrial control panels
Industrial control panels are crucial elements in automated systems and industrial installations, enabling complex processes to be supervised and managed. Their design and manufacture require careful attention to detail, both in terms of functionality and safety. These panels are used in sectors as varied as the automotive, energy, agri-food and infrastructure industries.
Industrial control panel manufacturing steps
Applications for industrial control panels
Control panels are used in a variety of industrial applications:
- Process supervision:
They can be used to monitor and regulate complex processes such as power generation, parts assembly, or control of manufacturing conditions. - Machine control:
In manufacturing plants, control panels supervise the operation of automated machines and industrial robots.
- Safety management:
Complex safety systems, such as alarms and emergency stops, are often integrated into control panels to protect workers and equipment. - Production line automation:
Control panels centralize commands and manage the automation of production lines, reducing dependence on human intervention.
Conclusion
Manufacturing industrial control panels is a highly specialized process, combining expertise in electricity, automation and safety. These panels play an essential role in the modernization of industrial processes, offering efficient and safe solutions for supervising complex operations. As automation and connectivity technologies advance, control panels continue to evolve, becoming increasingly intelligent and capable of integrating advanced management systems.
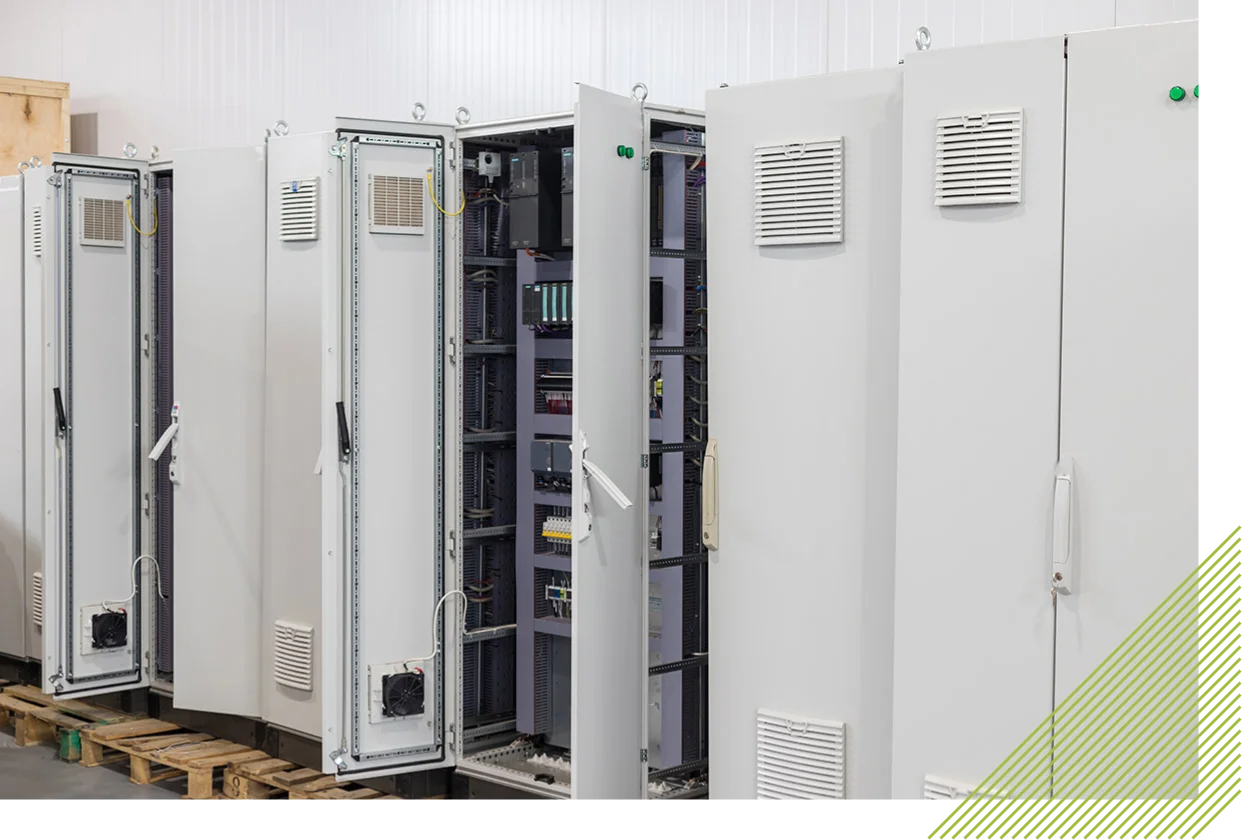