Automated vision systems in the industrial sector
Automated vision systems (or “machine vision”) have become indispensable in the industrial sector for improving productivity, precision and quality. They combine cameras, image processing software, and sometimes artificial intelligence (AI) algorithms to analyze, interpret and control processes in real time.
How automated vision systems work
These systems capture images or videos of products or processes in progress using specific cameras, often coupled with appropriate lighting to optimize image quality. The images are then analyzed by software which identifies important features, such as dimensions, colors, defects or shapes, according to pre-defined criteria.
For example:
- Quality inspection :
Identification of defects on industrial parts or food packaging. - Dimensional inspection:
Checking sizes and tolerances of mechanical parts. - Barcode or QR code reading:
Ensures traceability throughout the production chain.
Advantages of automated vision systems
- Increased accuracy:
These systems eliminate human error in visual inspection, enabling reliable defect detection even at high speeds. - Time efficiency:
Thanks to their ability to analyze hundreds of images per minute, they significantly increase production rates. - Improved quality:
By identifying defects at an early stage, they reduce the costs associated with non-conforming products or recalls. - Flexibility:
Modern systems can be quickly reprogrammed to adapt to new products or processes.
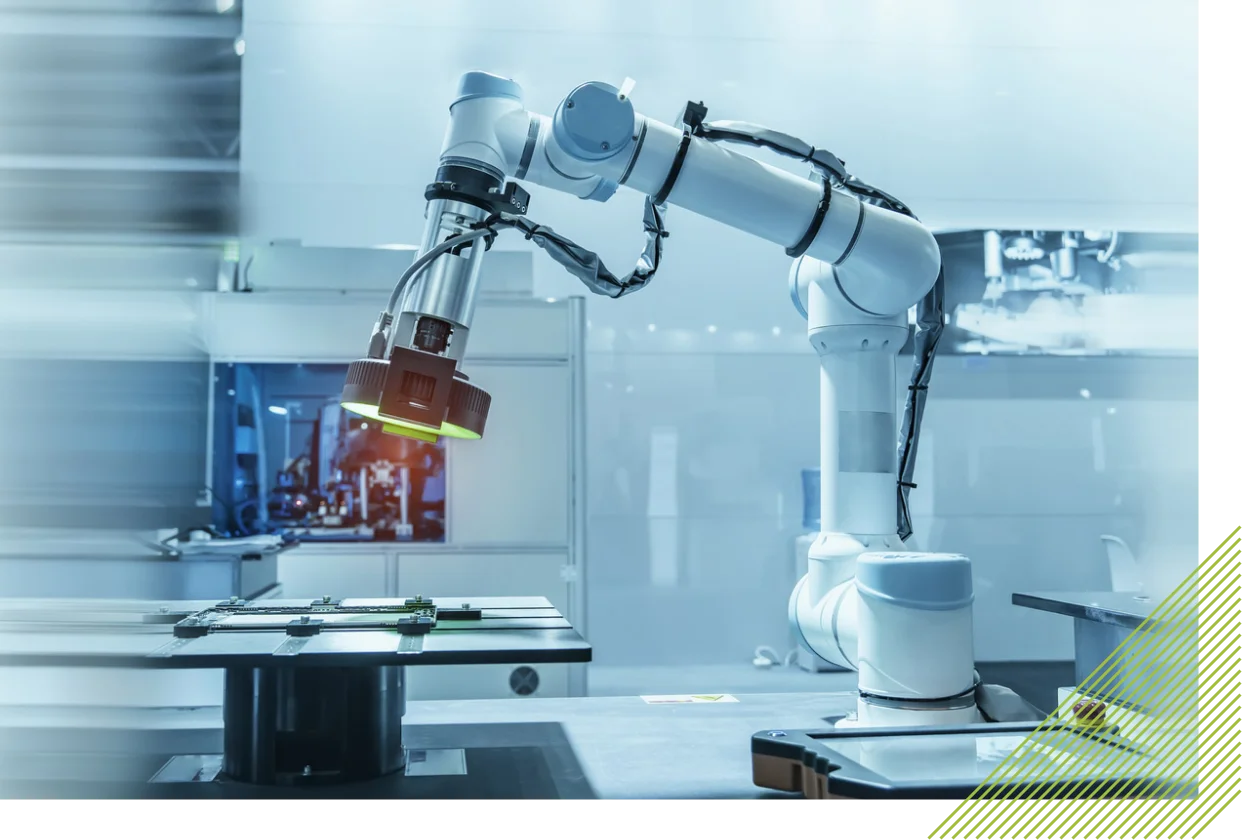
Applications in various industries
- Food industry:
Checking packaging integrity, inspecting products for contaminants or defects (e.g. damaged fruit). - Automotive:
Verification of components and assemblies, such as welds or machined parts. - Electronics:
Inspection of printed circuits and checking of connections to detect micro-defects. - Pharmaceuticals:
Checking the conformity of labels, caps or bottle filling.
Challenges and innovations
Ongoing challenges include efficient processing of large amounts of visual data, integration with other technologies (such as AI or industrial robots), and cost reduction for wider adoption. The latest innovations include the use of 3D cameras, machine learning techniques for more intelligent analysis, and embedded systems that operate in real time without the need for external servers.
Future prospects
As technologies rapidly evolve, automated vision systems will play a central role in Industry 4.0. Their integration with the Internet of Things (IoT) and predictive analysis systems will help anticipate problems and improve decision-making.
These tools do more than just “see”: they actively participate in the digital transformation of industries, making production lines more intelligent, connected and efficient.